To implement a Management System, you need to learn what’s required to be successful, and how to avoid common failures. A carefully planned and well executed implementation will help you avoid typical problems and greatly increase the value gained from your effort.
Six companies that had implementation failures
experienced the following impacts:
12-24 months of delays or re-work
$200,000-$1,500,000 in additional costs
Significant reduction in implementation effectiveness that frustrated Leadership and caused long-term impact and failure
SPAN is in a unique position of having intimate knowledge of many companies and their experiences implementing management systems. We are providing this business case to share our knowledge and help you avoid similar failures that others learned the hard way.
The six companies tell a compelling tale of success and failure. They are all large companies that committed significant resources to implementing a management system, but despite this, only two companies currently have a successfully implemented management system, three are only partially successful and one had a complete failure. We can't share the names and details of the companies, but we can assure you they are real and these are their stories.
All six companies had the same initial problems
Leadership lacked awareness and understanding of how the management system would benefit their company, leading to delayed commitment, initial budget cuts and timeline delays.
The companies spent too much time tweaking and over-thinking their management system framework design, which ate up valuable implementation budget, slowed momentum and put the entire implementation at risk.
Leadership were confused by multiple goals being added to the management system project such as operational excellence, safety culture, or commitments to zero incidents without first understanding how all these objectives fitted together in an integrated management system design.
Two of the companies got back on track
They identified and agreed on external regulations and standards such as API RP 1173, CER OPR and CFRs that needed to be met by the management system. As a result, they designed a framework with the necessary internal requirements to meet their needs as well as their desired culture.
The companies clearly defined leadership and employee responsibilities related to their management system, and then involved Leadership in validating the Pipeline Safety Management System framework design, further building Leadership ownership and enhancing their chance of success.
After completing well planned gap assessments, the companies developed a detailed implementation plan with communications, training and other activities clearly outlined, to provide Leadership with a clear and accurate roadmap that included timelines and budgets.
The four other companies continued to have significant problems
Four companies didn’t properly execute an organization-wide communication and training plan that is necessary to raise awareness, and support those Leaders and stakeholders responsible for management system implementation success.
Three companies didn’t undertake company-wide operational assessments that are critical to properly engage all stakeholders in the management system and enable employees to identify their own operational improvements. Opportunities to establish buy-in and solidify a culture of safety improvement were missed.
Three companies didn’t have a tool to facilitate assessments in a consistent manner and aggregate gaps and improvement actions in a secure, dependable system. Consequently, they drowned in their own data and were not capable of properly reporting the progress and performance of their management system.
Three companies didn’t have a leadership steering committee or adequate decision-making accountabilities and a system for prioritizing gaps, assigning improvement actions and holding employees accountable for success.
Three companies did not have an adequate process for integrating their improvement actions into regular company budgeting, execution and monitoring processes. A management system is not truly implemented until its continuous improvement cycle is aligned with a company's business cycle.
Check out our processes for successfully implementing Management Systems
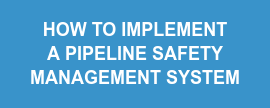
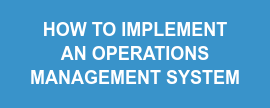
SPAN Resources
If you would like to see other case studies, management system white papers, and other useful content, please click here to access our resource library.